Crafting Excellence: The Manufacturing Process of Holographic PVC Mirror Bags
Time:2025-04-10
Views:8
Crafting Excellence: The Manufacturing Process of Holographic PVC Mirror Bags
PVC mirror bags, known for their eye-catching holographic finishes and durable design, are a popular choice in fashion and accessory markets. Here’s a step-by-step breakdown of how these sleek, reflective bags are made:
1. Material Selection & Preparation
High-quality PVC sheets are carefully selected for their flexibility, durability, and ability to hold vibrant prints. The sheets are cleaned and treated to ensure a smooth base for printing and finishing.
2. Design Printing
Advanced digital printing techniques transfer intricate designs, patterns, or logos onto the PVC surface. UV inks are often used for their resistance to fading and ability to adhere to the glossy material. Silkscreen printing is used for the simple logo.
3. Cutting & Shaping
Precision cutting machines shape the PVC sheets into bag components (front/back panels, straps, etc.). Laser cutting ensures sharp edges and consistent sizing for a professional look.
4. Assembly
Components are assembled using high-strength stitching or ultrasonic welding. Reinforced stitching and durable hardware (zippers, buckles) are added to ensure longevity.
5. Quality Control
Each bag undergoes rigorous checks for print alignment, structural integrity, and functionality. Waterproof and abrasion resistance tests are performed to meet industry standards.
6. Packaging & Customization
Finished bags are carefully packaged, with options for custom branding (tags, inserts) to cater to retail or wholesale needs.
Why Choose PVC Mirror Bags?
Combining style, durability, and versatility, these bags are ideal for fashion-forward consumers seeking bold, modern aesthetics. Their water-resistant properties and lightweight design make them perfect for everyday use or special occasions.
Optimize your accessory line with premium PVC mirror bags—where cutting-edge craftsmanship meets unstoppable style.
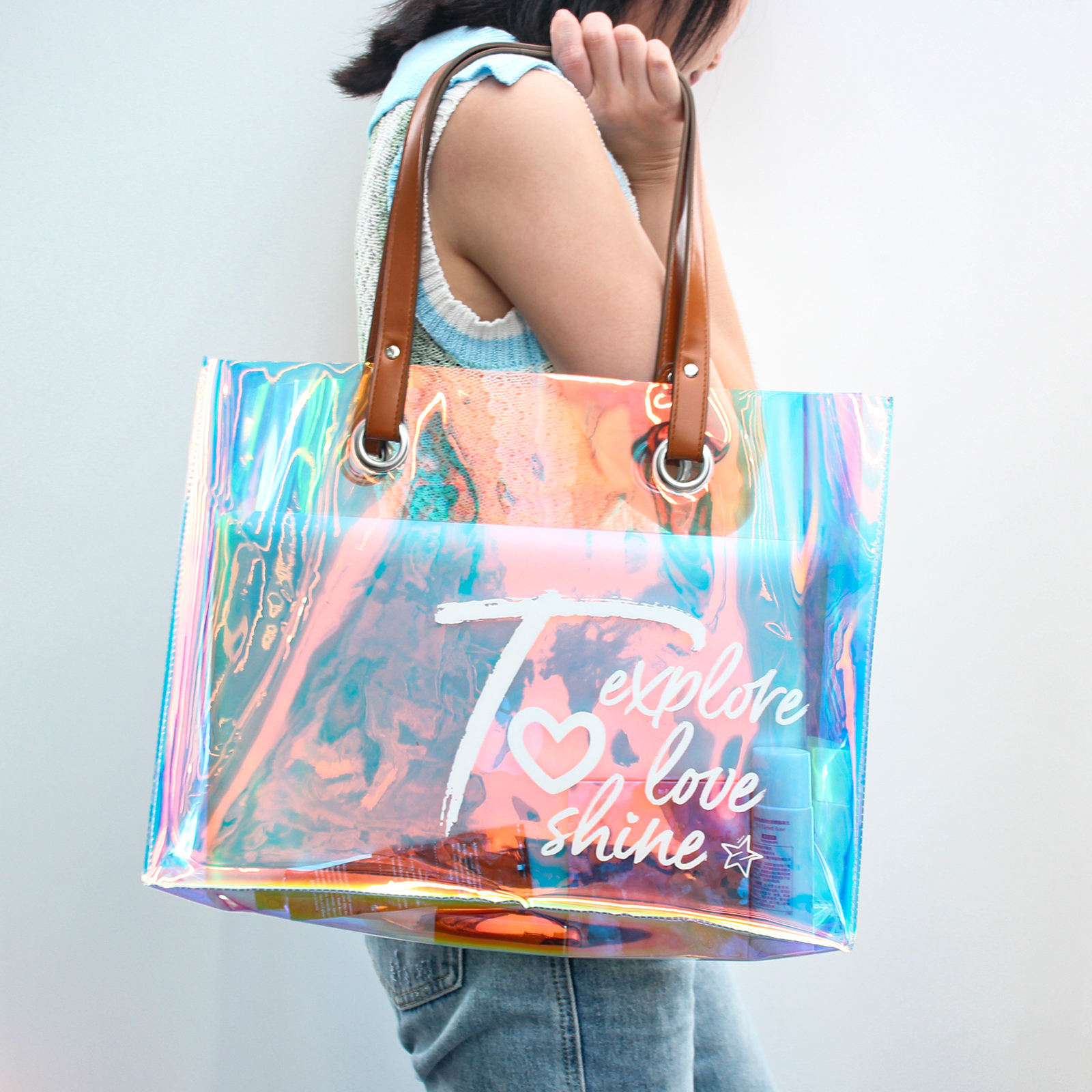
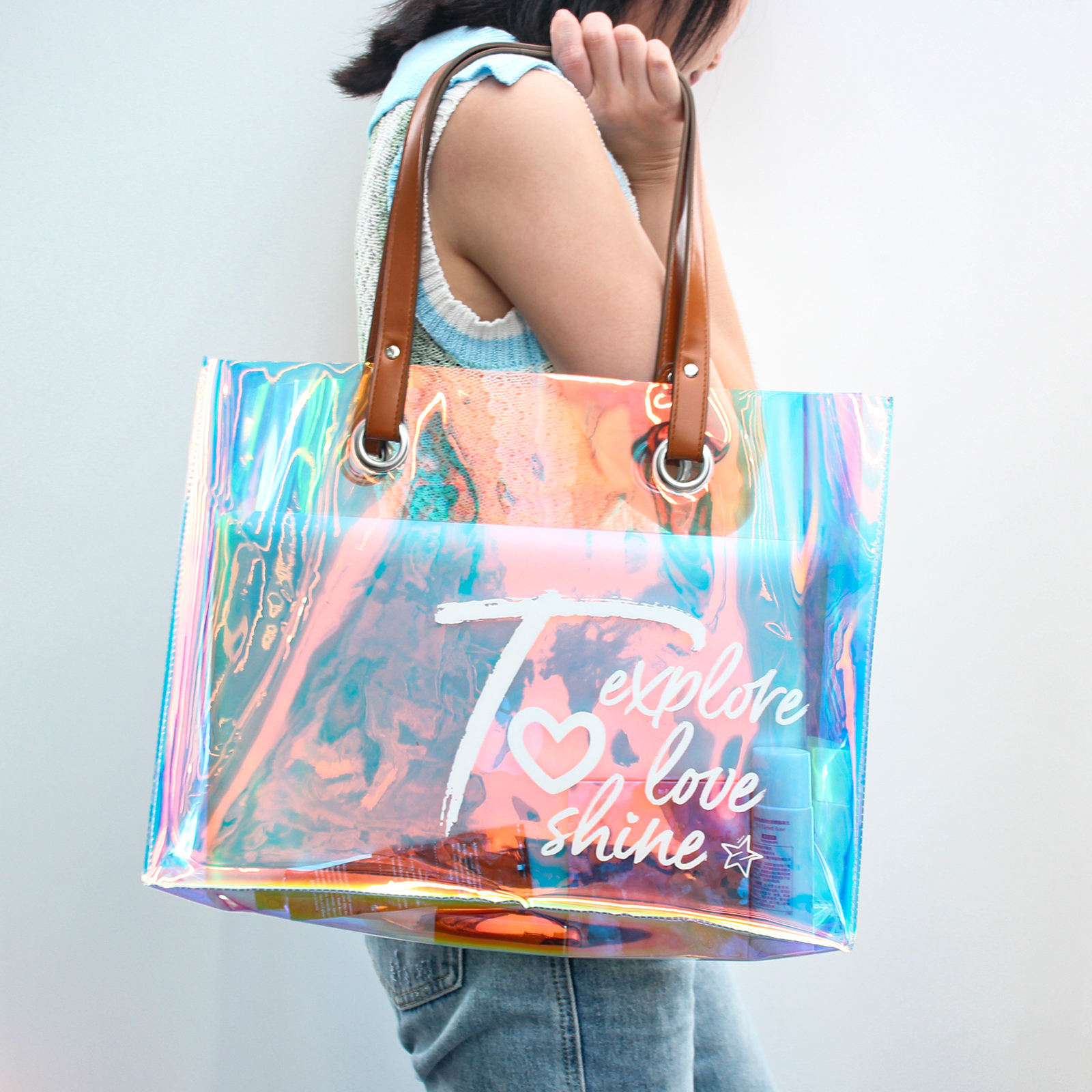